Choosing a construction system is one of the key decisions that real estate developers have to make in order to reduce cost, shorten delivery time, and build sustainable homes for the future.
Owning a home is a huge milestone achievement for many people, but achieving this dream is usually hindered by many obstacles, the estimating the cost of construction being the most intimidating. As the cost of building materials continues to rise, how can developers help homeowners afford homes while remaining competitive? The rise of Industrialized Construction (IC) brings a new chapter in affordable housing. IC companies use innovative building systems such as prefabricated and modular homes that are cheaper, sustainable, and energy efficient. IC will bring the dream of owning a home closer to reality for aspiring homeowners.
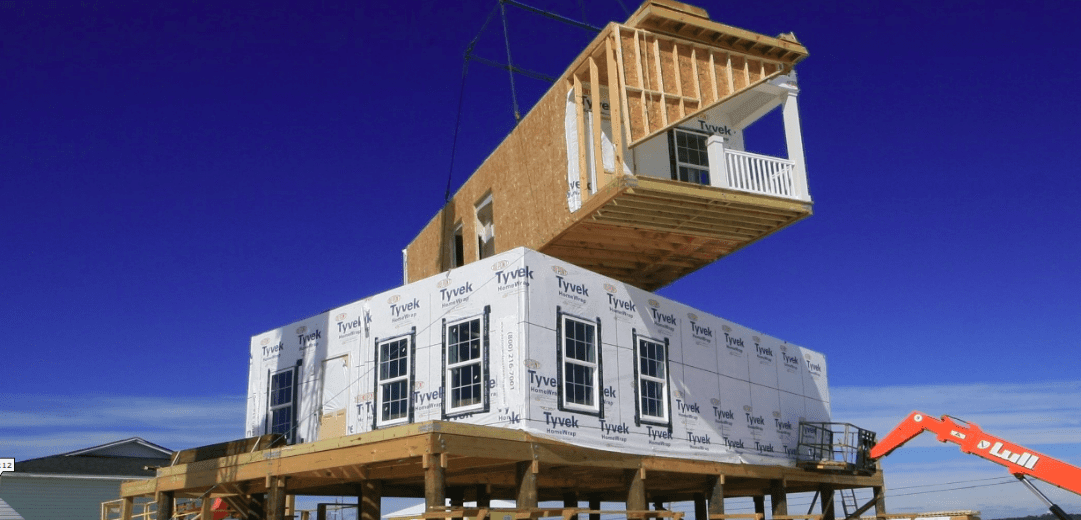
This article looks at the landscape of future homes and the new innovative building systems being employed in their construction.
Traditional stick-built houses are expensive to construct, and the cost of raw materials continues to rise. The cost of construction is often high, a lot of labour is required, the build times are long, and adverse weather can stall the project. This method of construction eventually leaves a ton of waste, which is bad for the environment. Additionally, production of raw materials used for conventional formworks such as cement are known to produce at least 20% of global carbon emissions. Future homes as a concpet is the effort towards new greener, cheaper building systems that has evolved into a popular topic in real estate development circles and among homeowners and tech bloggers. It revolves around new building systems and formworks, and involves Industrialized Construction techniques.
Industry stakeholders and governments are increasingly collaborating in the process of creating standards to define requirements for new homes. On 1 October 2019, the Ministry of Housing, UK, published the Future Homes Standards [4], that sets requirements for new constructions.
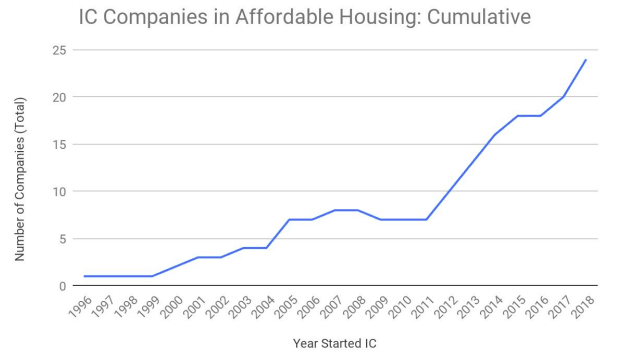
Future Homes – What defines it?
In general, while standards may vary slightly from group to group, and expectations from person to person, the main characteristics of future homes remain the same, which is industrialized construction. This largely covers modular homes, aka prefabricated homes or manufactured homes.
Additionally, developers of future homes aim at minimizing the building’s impact on the environment, and this concern is integrated into the project, right from the design phase, selection of materials to the energy efficiency of the building. Net zero energy, net zero water, and net zero carbon concepts are made part of design process, to produce houses that have zero impact on the environment.
One way to achieve this goal is to blend the design of the house with the geography of the construction site, and an excellent example is the Villa Ypsilon in Greece built in 2017 by Theo Sarantoglou Lalis architects, with locally sourced materials, and has a breathtaking front elevation.
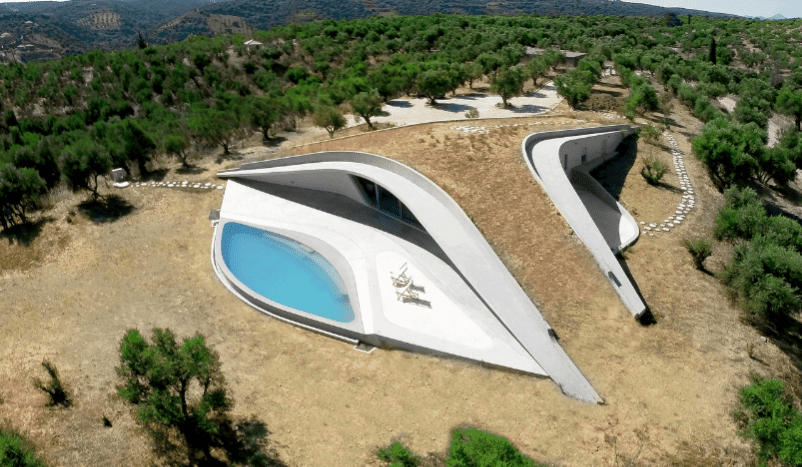
As property prices continue to rise, innovative designers maximize the use of available space with designs such as this futuristic green roof of the Sky Garden House in Singapore. The design provides a greater outdoor experience than a regular home.
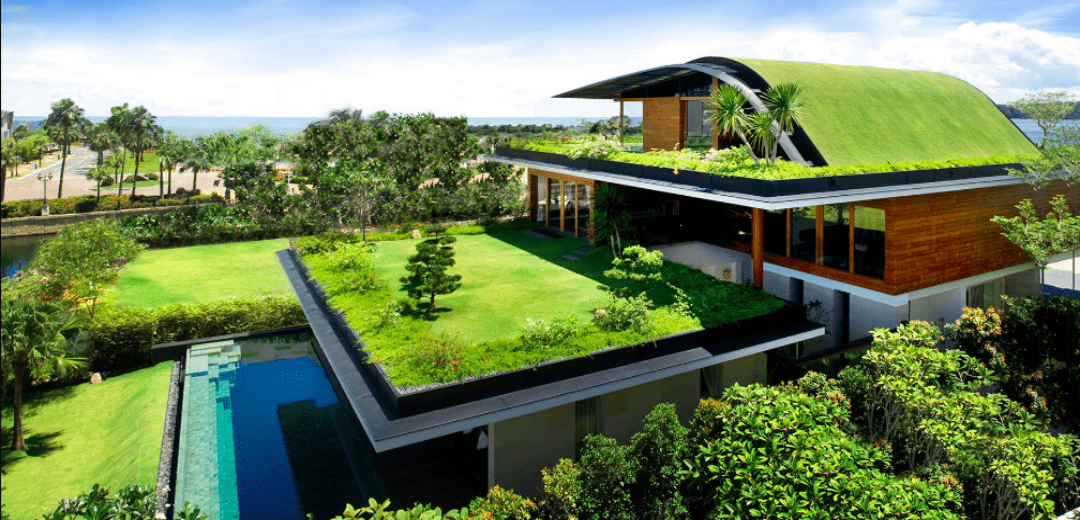
Industrialized construction (IC)

Unlike general manufacturing, the construction industry has largely relied on manual and field labour, and has thus remained at low levels of productivity with high costs of production. However, industrialization of the industry is steady, with more major investment being made between 2010 and 2021.
Industrialized construction (IC) is the prefabrication of modular units in controlled factory environments, and promotes the use of mechanisation and technology to improve productivity. Software modeling tools such as Autodesk Revit are used to create 3D models of individual floors, rooms, and smaller components like electrical and plumbing modules. These are then prefabricated carefully indoors, and are thus referred to as manufactured homes. Being built in pieces that are assembled later gives these future homes their other name, modular homes. However, not all IC built houses are modular.
IC is a well adopted approach in real estate development today. According to market research, modular and prefabricated buildings accounted for roughly $237 billion of construction in 2019. As can be seen from this chart (Pullen Lessing, 2019), the number of IC companies has increased sharply in the last decade.
By 2035, most buildings will be constructed through IC, according to the AutoDesk Industrialized Construction Report. The report also cited a study by McKinsey that showed that large projects typically extend 20 percent beyond the initial project completion date, and they are usually up to 80 percent over budget. This statistic alone is motivation for developers to move towards IC. Skanska and IKEA jointly developed the BoKlok homes concept. Their homepage states that “Boklok homes are built primarily from wood, using a smart, industrialised and efficient process. Homes are completed off-site in a safe and dry environment using modern methods of construction.”
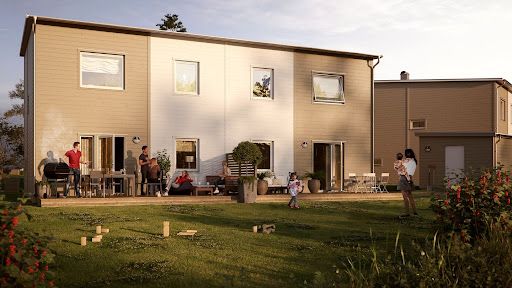
A Boklok home.
IC – Manufactured and Modular Future Homes
Modular units of a house are built offsite in controlled indoor factory environments. Installation of fixtures, plumbing and wiring are done at the factory, rather than on-site, and thus cannot be stalled by adverse weather. Complete modules transported to the site with specially designed vehicles, and then installed on permanent foundations.
Industrial mechanization equipment such as cranes are used throughout the building process. Modular homes have the benefit of being customizable, and require short build times. They are usually constructed in units of similar size to ease transportation and installation, but the floor plans can be as varied as the homeowner desires.
The Old – Traditional Formworks
Conventionally, formwork is made from wood and steel, but these traditional materials have their problems. For example, timber, which is among the oldest materials for constructing formwork, is popular due to its availability, but it shrinks, swells and warps underweight and cannot be reused many times. IC companies are moving to newer alternatives, and we shall look at several of them below. On the other hand, steel, which is stronger and more durable, is rather expensive for most home projects.
Future Homes – Formworks for new in Industrial of Construction
Construction of future homes involves the use of formworks that are custom designed to provide many benefits such as thermal insulation, resistance to the weather, fire resistance, and can be easier to work with. Using these formworks results in shorter build times and lower construction costs. Let us look at some of them.
Insulated Concrete Formworks (ICFs)
ICFs are a system of strong and energy efficient reinforced concrete forms. They insulated materials made with thermal installations to increase the building’s energy efficiency. ICFs are stacked together before being filled with concrete, and stay in place as a permanent exterior layer. The building is then adorned with traditional finishes and looks just like any other house. ICFs are disaster and fire resistant, and provide for shorter building times.
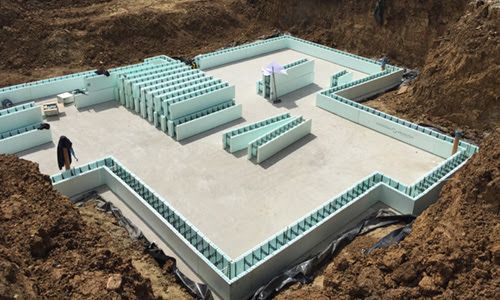
Autoclaved Aerated Concrete (Aircrete)
Aircrete is green formwork made from natural materials such as sand and cement, while the faces are bound with gypsum binders and aluminium is used as an aerating agent. They are moulded in steam-heated autoclaves to support the strengthening chemical reactions and are lightweight, provide insulation and strength. Aircrete formworks are fire resistant, and can be installed in a matter of days.
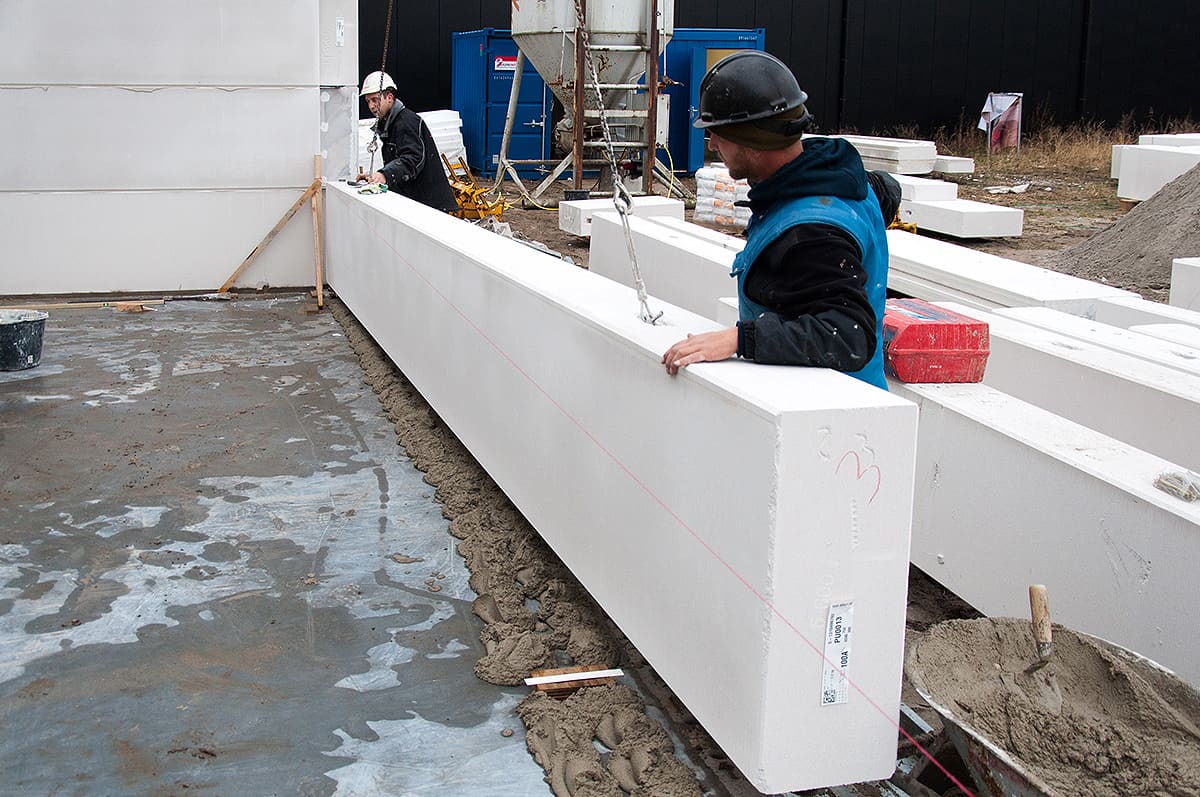
Superior Walls
Another building system used by designers and developers of future homes is wall panel systems, also known as superior walls. They are precast concrete panel systems, typically used for foundation walls and are custom-designed to provide homeowners with strong, warm and dry basements. They can also be used for above ground construction.
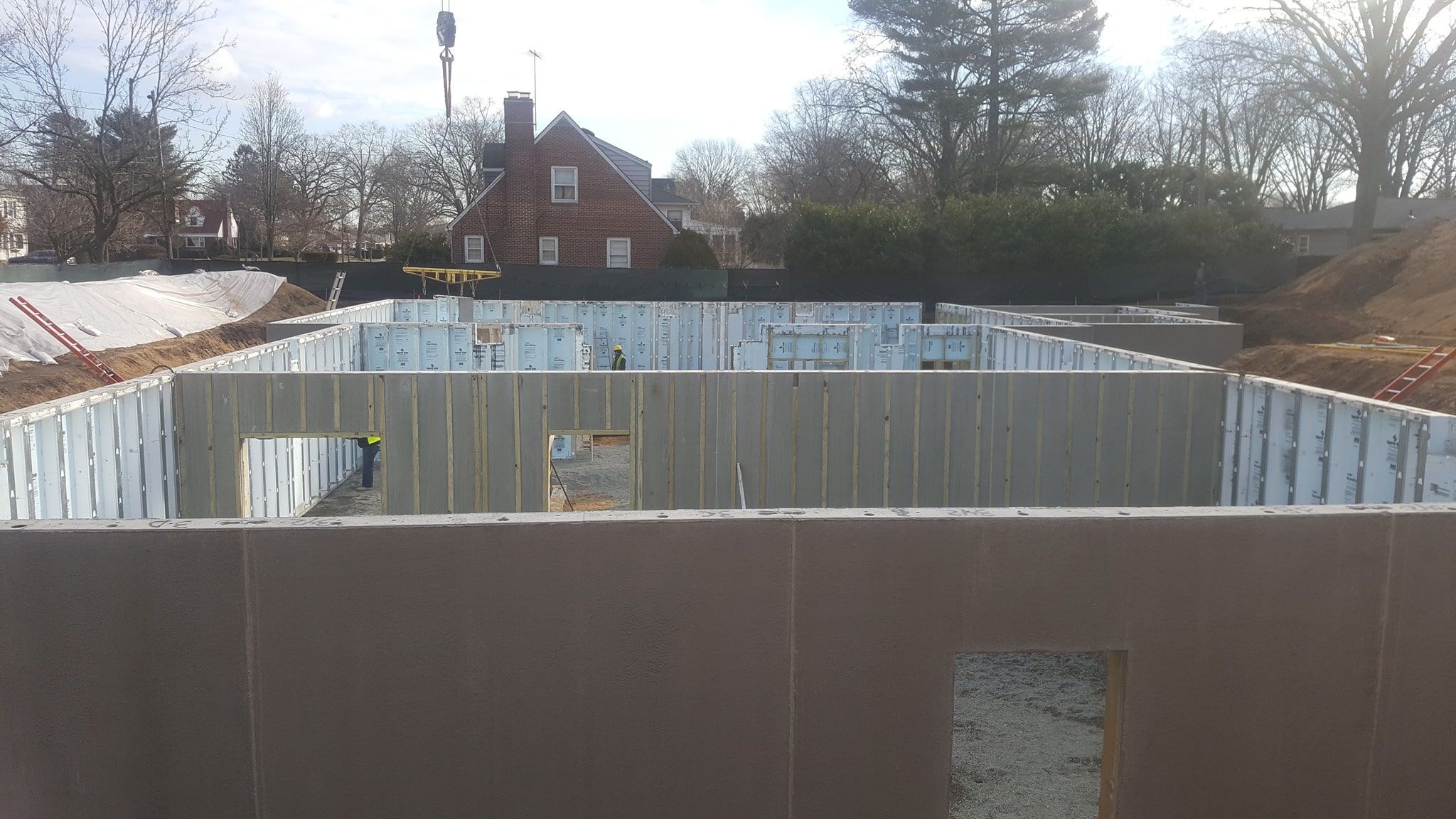
Permaform
Permaform is a permanent multi purpose formwork system for foundations and slabs, but can also be used as sheeting for building pits or as a dust protection screen. It is easy to lay by hand and comes in varying thickness, and can be shortened and adapted on the building site using simple tools. Other advantages are that it is easy to transport and handle and can be installed quite quickly, saving time and storage.
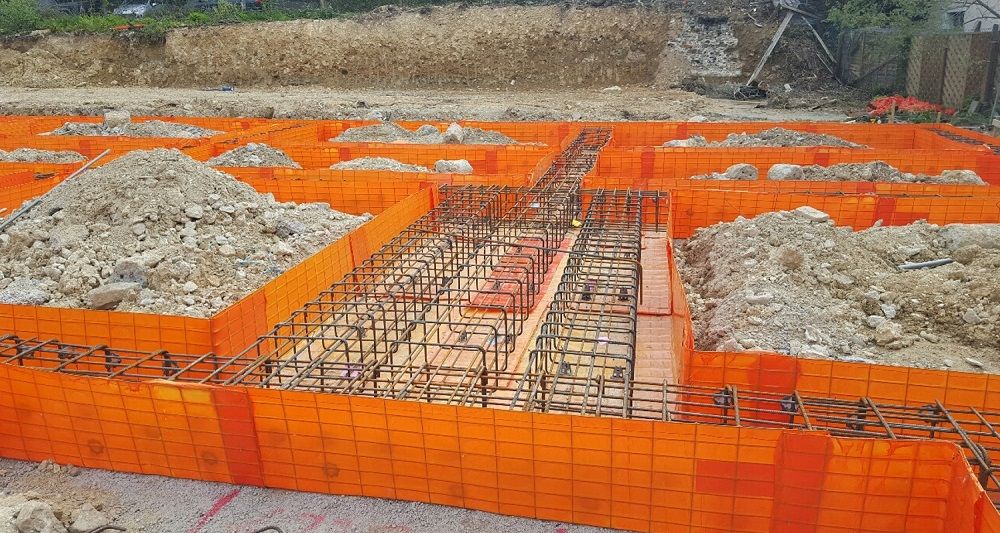
Plastic Formwork
With benefits such as durability, flexibility and low cost, PVC plastic formworks are available for fast and cost effective construction. They are held together by binders, and then supported with timber or other material before concrete is poured. The resulting walls are smooth and require minimal work before painting.
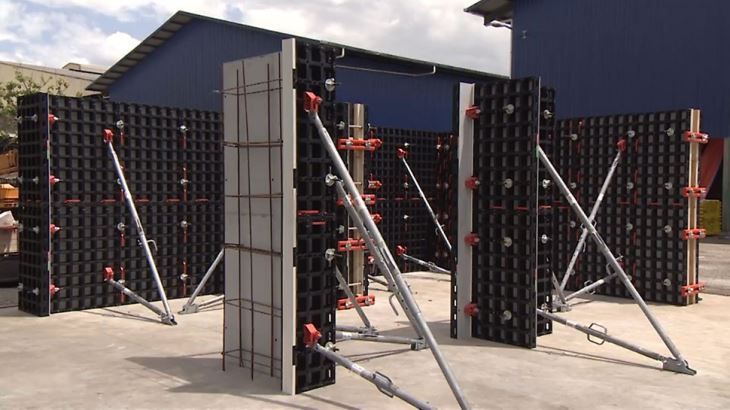
Spider Tie
Spider Tie is a flexible formwork designed for multiple applications such as walls, swimming pools and roofs. They consist of a framework to which plywood is then attached to produce the desired shape. They hold the rebars in place without the need for tie-wire.
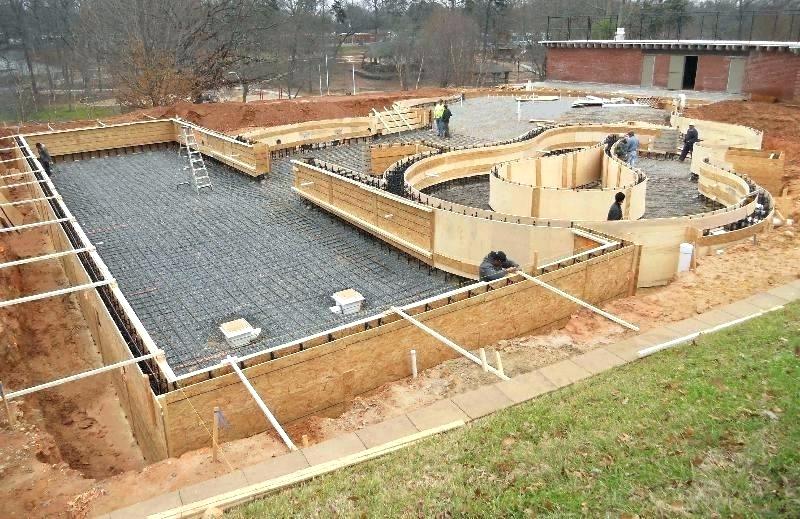
The Future of Future Homes
More developers are expected to start easing into Industrialized Construction (IC), and the trend of adopting these innovative building systems, continues to grow. IC will make the industry more productive and profitable, owing to lower construction costs, which is a great win for homeowners. IC will also reduces the impact of the built area on the environment, as more futuristic homes are built.
What’s Next?
Has your team built a future home before? Have you ever considered using any of the formworks and building systems discussed above? Do you know of any other building system I have not mentioned? Please share your experience building future homes in the comments section below, and let us learn from one another!
Also visit our blog to learn more about architecture.